Location:
|
Livermore, California
|
Accident Number:
|
WPR22LA174
|
Date & Time:
|
May 11, 2022, 09:30 Local
|
Registration:
|
N999GH
|
Aircraft:
|
BELL HELICOPTER TEXTRON
|
Aircraft Damage:
|
Substantial
|
CANADA 407
|
|
|
|
Defining Event:
|
Miscellaneous/other
|
Injuries:
|
1 Serious, 1 Minor
|
Flight Conducted Under:
|
Part 133: Rotorcraft ext. load
|
|
|
|
Analysis
The pilot was performing a human external cargo (HEC) long-line qualification exam flight at the training operations facility of a public utility company. After performing the initial maneuvers, the pilot transitioned to the HEC phase of the exam by carrying a lineman on a 60-ft long line. While maneuvering the helicopter at an altitude of about 175 ft above ground level (agl), the helicopter lost engine power. In response, the pilot selected what he thought was the “emergency” throttle detent, but the engine did not respond. The pilot maneuvered the lineman away from the landing helicopter and performed an autorotation. The helicopter landed hard and sustained substantial damage. The pilot sustained serious injuries and the lineman sustained minor injuries.
A complete postaccident examination of the airframe, engine, and engine control systems did not reveal any evidence of preimpact mechanical malfunction or failures. The helicopter contained fuel, was loaded within its envelope, and weather was not a factor.
The engine was test run in a test cell and it performed nominally. Onboard video recorded a section of the annunciator panel that showed some, but not all, engine warning lights, none of which illuminated at any point during the flight. The recording did capture an audio tone as the descent began that was the same frequency as the engine out and low rotor warning indicators.
Review of data recorded by the engine control unit (ECU) revealed that at the time of the loss of engine power, the throttle was in the “IDLE” rather than the “FLY” position as would have been required during flight. A few seconds later, the throttle position moved back into the “FLY” range.
The pilot was flying the helicopter solo from the right seat with the door removed so that he could lean outside and observe below. The collective control, which housed the engine throttle twist grip at its end, was mounted on the pilot’s left side. The direction of throttle rotation meant that if the pilot maintained a tight grip on the throttle as he leaned right and out of the helicopter, the direction of throttle rotation was such that his hand could have inadvertently rolled the throttle out of FLY and into IDLE. Under this scenario, the engine would lose power immediately; both audio and engine diagnostic data confirmed this had likely happened. The pilot almost immediately rolled the throttle back into the FLY position but the design of the engine control system was such that it assumed the helicopter was on the ground and therefore limited power application to prevent an over-torque condition. So, even though the pilot immediately remedied the problem, the engine would not have regained power. The pilot stated as soon as he noticed a loss of power he moved the throttle beyond “FLY” and to the “emergency” position. However, although this position could be selected, it had no function on this type of helicopter; it was a hold out from the previous version of the helicopter that the pilot had flown. This mistake had no bearing on the accident and would not have affected the outcome.
The HEC operation required that the helicopter be flown at a low height and speed such that it was operating within the “AVOID” range of its Height-Velocity Envelope. In this range, a safe landing could not be guaranteed following an engine failure. Additionally, the nature of the training facility, with multiple training towers and obstacles in the immediate vicinity, further reduced the likelihood of a successful outcome in the event of an emergency. Therefore, although the pilot made the mistake of inadvertently shutting down the engine in flight, he was still able to demonstrate the presence of mind and helicopter control to maneuver the helicopter away from the lineman and into an open area.
This was the second time the pilot had taken the HEC exam, having failed the first attempt. The video recording appeared to show the pilot was anxious throughout the flight; however, considering the nature of the work he was performing and the stress he would have been experiencing, this is understandable. It could not be determined if this contributed to the accident.
Probable Cause and Findings
The National Transportation Safety Board determines the probable cause(s) of this accident to be:
Loss of engine power due to the pilot inadvertently selecting engine IDLE mode while in flight, which reduced rotor and engine speed to a level that could not sustain flight.
Findings
Aircraft (general) - Unintentional use/operation
Personnel issues Use of equip/system - Pilot
Personnel issues Incorrect action performance - Pilot
Factual Information
History of Flight
Maneuvering-hover Engine shutdown
Maneuvering-hover Miscellaneous/other (Defining event)
Emergency descent Collision with terr/obj (non-CFIT)
On May 11, 2022, about 0930 Pacific daylight time, a Bell Helicopter Textron Canada 407, N999GH, was substantially damaged when it was involved in an accident near Livermore, California. The pilot was seriously injured and the lineman crew member sustained minor injuries. The helicopter was operated as a Title 14 Code of Federal Regulations Part 133 rotorcraft external-load flight.
The pilot was performing a HEC long-line qualification exam flight at the Livermore Electric Safety Academy, a training operations facility owned by the Pacific Gas and Electric Company (PG&E). The pilot was flying the helicopter solo from the right seat with the door removed so that he could lean outside and observe below. The maneuvers were observed and monitored on the ground by a group of examiners.
The pilot stated that the first 20 minutes of the flight were normal and the accident occurred during the final phase while carrying a PG&E lineman on a 60-ft long line. The pilot was maneuvering the helicopter at an altitude of about 175 ft agl, positioning the lineman against a static line marker ball midway along a 90-ft wire that spanned an 88-ft lattice tower and a 65-ft wood pole. The pilot reported that the engine then lost power and he rolled the throttle out of the “FLY” detent and into the “emergency” range, but the engine did not respond.
He attempted to maneuver the lineman into a clearing and partially raised the collective once the lineman was about 15 ft agl to cushion the lineman’s landing. The pilot stated that he then maneuvered the helicopter to a landing spot away from the linemen and, after reaching an altitude of about 30 ft agl, he raised the collective and dropped the HEC line and cargo hooks; the helicopter landed hard. The pilot stated that the engine was still running after landing and he was able to then shut off the main fuel valve and battery. He was extricated from the helicopter about 30 minutes later.
Multiple witnesses recounted observations that matched the pilot’s statement. All stated that the helicopter appeared to be operating without issue throughout the maneuvers until they heard a change in engine tone, with some then observing the main rotor blades slowing as the helicopter began to rapidly descend. A video provided by a witness showed the helicopter descending just before impact. It appeared intact and was not emitting smoke or vapors.
Pilot Information
Certificate:
|
Commercial; Flight instructor
|
Age:
|
38,Male
|
Airplane Rating(s):
|
None
|
Seat Occupied:
|
Right
|
Other Aircraft Rating(s):
|
Helicopter
|
Restraint Used:
|
4-point
|
Instrument Rating(s):
|
Helicopter
|
Second Pilot Present:
|
No
|
Instructor Rating(s):
|
Instrument helicopter
|
Toxicology Performed:
|
|
Medical Certification:
|
Class 2 Without
|
Last FAA Medical Exam:
|
March 29, 2022
|
|
waivers/limitations
|
|
|
Occupational Pilot:
|
Yes
|
Last Flight Review or Equivalent:
|
February 19, 2022
|
Flight Time:
|
3475 hours (Total, all aircraft), 175 hours (Total, this make and model), 3420 hours (Pilot In
|
|
Command, all aircraft)
|
|
|
The pilot reported about 3,500 hours of total flight experience including about 1,000 hours as a flight instructor and agricultural pilot. He started working for the helicopter operator about 15 months before the accident. He reported a total of almost 175 hours flight experience in the Bell 407, 10 of which were in the Honeywell engine-equipped 407HP version, all in the accident helicopter.
The pilot’s total FAR Part 133 external load time before the accident totaled about 87 hours. Most of the flight time took place in the Eurocopter AS-350, with 2.3 hours in the Bell 407, and 6.7 hours in the 407HP. Two of the flights involved HEC, with all other flights involving training or carriage of cargo or buckets, all flown from the right seat.
The accident flight was a demonstration flight to PG&E so he could be signed off to perform HEC flights for them. According to the helicopter operator, this was the second time he had taken the check ride, having not passed on the first attempt.
The night before the accident he stayed in a hotel and went to bed about 2100. He awoke at 0630 and reported having a normal night sleep and was well rested. The pilot was 6 ft tall.
Aircraft and Owner/Operator Information
Aircraft Make:
|
BELL HELICOPTER TEXTRON
|
Registration:
|
N999GH
|
|
CANADA
|
|
|
Model/Series:
|
407 HP
|
Aircraft Category:
|
Helicopter
|
Year of Manufacture:
|
2008
|
Amateur Built:
|
|
Airworthiness Certificate:
|
Normal
|
Serial Number:
|
53868
|
Landing Gear Type:
|
None; Skid
|
Seats:
|
7
|
Date/Type of Last
|
April 25, 2022 Continuous
|
Certified Max Gross Wt.:
|
5250 lbs
|
Inspection:
|
airworthiness
|
|
|
Time Since Last Inspection:
|
48.6 Hrs
|
Engines:
|
1 Turbo shaft
|
Airframe Total Time:
|
4055 Hrs as of last inspection
|
Engine Manufacturer:
|
Honeywell
|
ELT:
|
C126 installed, activated, did
|
Engine Model/Series:
|
HTS900-2-1D
|
|
not aid in locating accident
|
|
|
Registered Owner:
|
Guardian Helicopters
|
Rated Power:
|
900 Horsepower
|
Operator:
|
Guardian Helicopters
|
Operating Certificate(s)
|
Rotorcraft external load
|
|
|
Held:
|
(133)
|
Operator Does Business As:
|
Guardian Helicopters
|
Operator Designator Code:
|
|
In 2019, the helicopter was converted from its original Rolls Royce 250-C47 engine to a Honeywell HTS900-2-1D. The conversion was performed in accordance with the Eagle Copters, Eagle 407HP supplemental type certificate (STC) SR03496NY.
The Honeywell engine was controlled by a Full Authority Digital Engine Control (FADEC) system consisting of two redundant electronic control units (ECUs) along with a fuel metering unit (FMU) assembly, permanent magnet alternator, and other engine and airframe sensors. The FADEC system was designed to provide automatic control of the engine during startup, steady state, and transient operation and ensure that operation stayed within specified envelopes.
Pilot-commanded throttle position was monitored by the ECUs through a dual linear variable differential transformer (LVDT) assembly, mounted to the airframe and connected through a series of bellcranks to a conventional twist grip in the collective control column.
The helicopter was configured for operation from the right seat, with the collective control on the pilot’s left side. The twist grip had three distinct detent positions: OFF, IDLE, FLY, and an unmarked over-center position beyond FLY. Although it was available, this over-center position had no functional use in the Honeywell engine-equipped version of the helicopter. In the original Rolls-Royce engine-equipped helicopter, the over-center position was marked as the “MaxNG” detent. This position allowed the pilot to manually maintain main rotor/power turbine
(Nr/Np) speed by going beyond the FLY (90% gas producer [Ng] speed) detent in the event of a FADEC failure.
For both configurations, to reduce engine power, rotating the twist grip from FLY to IDLE would have required a rotation in the clockwise direction when facing forward. Additionally, a lockout button was included that needed to be pressed to move the control from IDLE to OFF.
Meteorological Information and Flight Plan
Conditions at Accident Site:
|
Visual (VMC)
|
Condition of Light:
|
Day
|
Observation Facility, Elevation:
|
KLVK,393 ft msl
|
Distance from Accident Site:
|
5 Nautical Miles
|
Observation Time:
|
09:53 Local
|
Direction from Accident Site:
|
266°
|
Lowest Cloud Condition:
|
Clear
|
Visibility
|
10 miles
|
Lowest Ceiling:
|
None
|
Visibility (RVR):
|
|
Wind Speed/Gusts:
|
4 knots /
|
Turbulence Type
|
/
|
|
|
Forecast/Actual:
|
|
Wind Direction:
|
|
Turbulence Severity
|
/
|
|
|
Forecast/Actual:
|
|
Altimeter Setting:
|
30.24 inches Hg
|
Temperature/Dew Point:
|
14°C / 3°C
|
Precipitation and Obscuration:
|
No Obscuration; No Precipitation
|
|
Departure Point:
|
Livermore, CA
|
Type of Flight Plan Filed:
|
None
|
Destination:
|
Livermore, CA
|
Type of Clearance:
|
None
|
Departure Time:
|
09:00 Local
|
Type of Airspace:
|
Class G
|
Airport Information
Airport:
|
PG&E LIVERMORE TRAINING
|
Runway Surface Type:
|
Asphalt
|
|
CENTER LA22
|
|
|
Airport Elevation:
|
572 ft msl
|
Runway Surface Condition:
|
Dry
|
Runway Used:
|
H
|
IFR Approach:
|
None
|
Runway Length/Width:
|
48 ft / 48 ft
|
VFR Approach/Landing:
|
Forced landing
|
Wreckage and Impact Information
Crew Injuries:
|
1 Serious, 1 Minor
|
Aircraft Damage:
|
Substantial
|
Passenger
|
N/A
|
Aircraft Fire:
|
None
|
Injuries:
|
|
|
|
Ground Injuries:
|
|
Aircraft Explosion:
|
None
|
Total Injuries:
|
1 Serious, 1 Minor
|
Latitude,
|
37.699413,-121.70852
|
|
|
Longitude:
|
|
The helicopter came to rest on its belly and was tilted slightly to the left (see Figures 1 and 2). The landing skids had spread outwards on both sides. The primary airframe structure was largely intact but had buckled in the roof area below the main transmission, which had moved out of position and was tilted slightly down. All four main rotor blades remained attached to the hub assembly; one blade was essentially undamaged and the remaining three had sustained delamination, aft bending, and buckling damage from midspan outwards. The tailboom remained attached to the aft bulkhead, and both tail rotor blades had detached with their roots remaining on the hub.
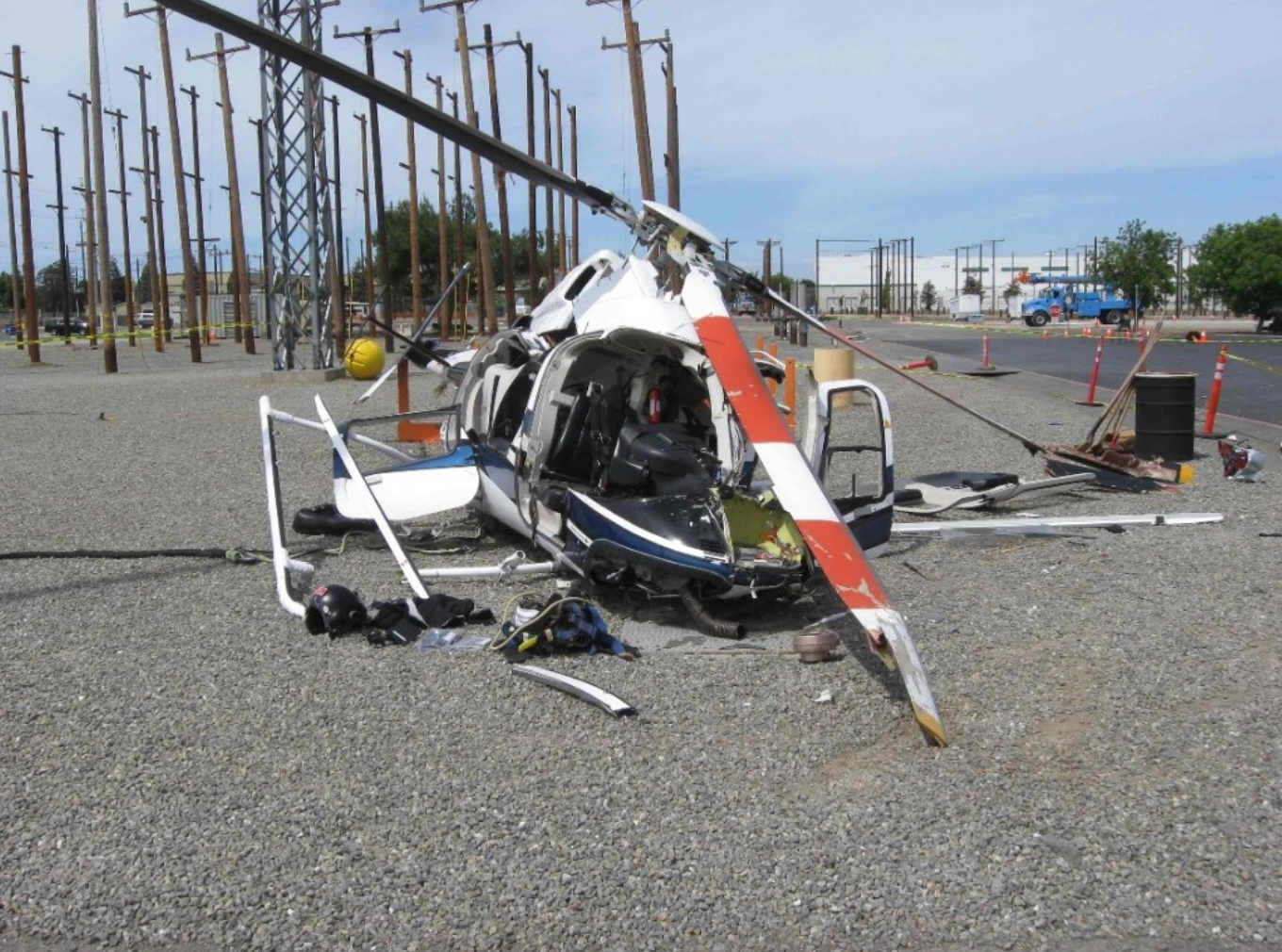
Figure 1– Helicopter at the accident site (photo courtesy of the FAA).
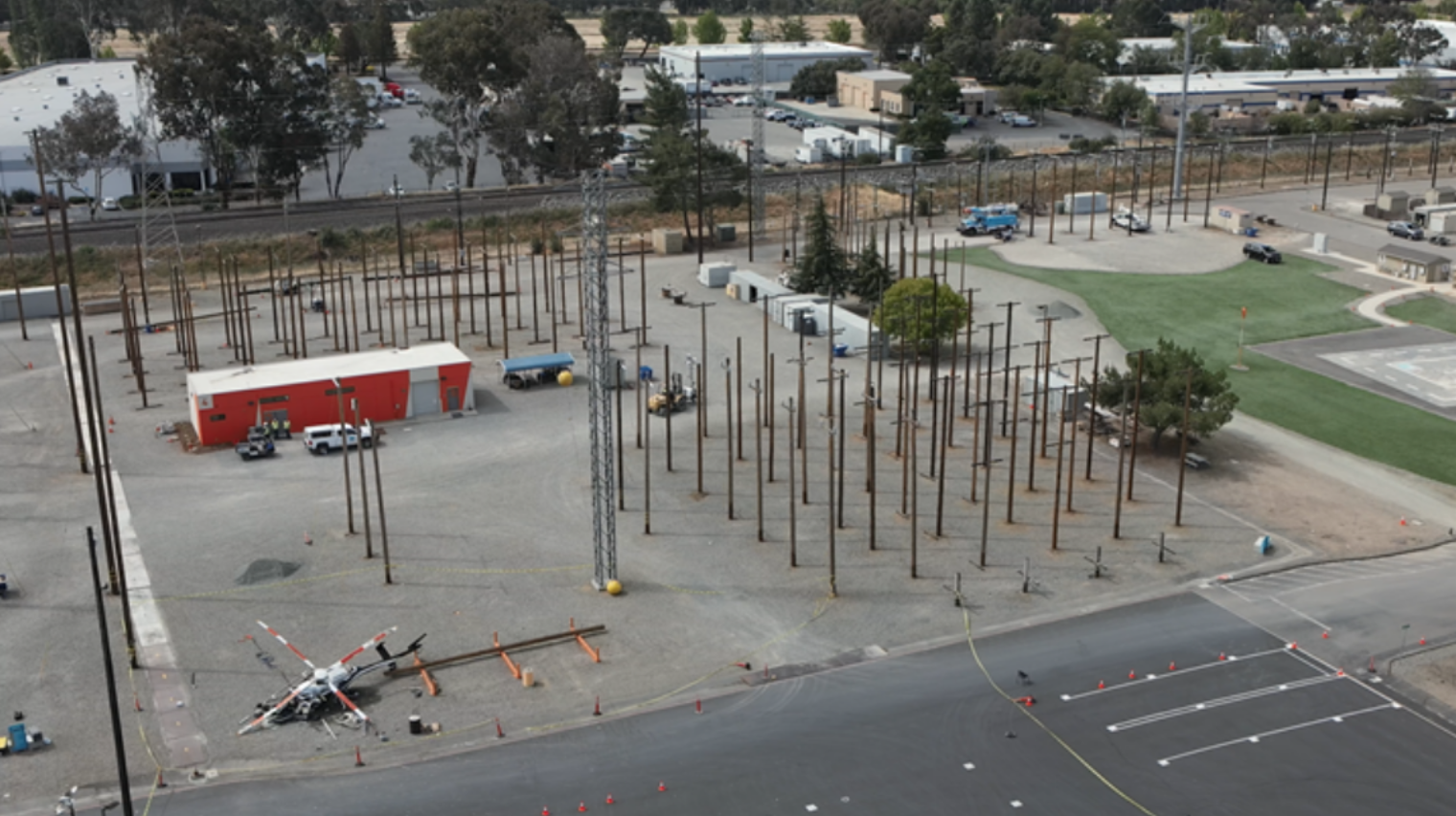
Figure 2 - Accident location within training facility (photo courtesy of PG&E).
The engine was still attached to its mounts and appeared to have sustained minimal damage. The engine output drive coupling had separated where it joined the main transmission. The damage to the coupling appeared to be consistent with movement of the main transmission at impact. There was no evidence of catastrophic engine failure or foreign object ingestion.
The transmission drivetrain was continuous from the engine output drive coupling through to the main gearbox and both the tail and main rotor blades; the freewheeling clutch was operational.
The flight controls sustained damage consistent with impact at the base of the main transmission assembly and the pilot’s collective control but were otherwise intact.
Flight recorders
Video
The helicopter was equipped an Appareo Vision 1000, which was a self-contained image, audio, and parametric data recorder. The parametric data included GPS aircraft time, position, altitude and speed, along with 3-axis acceleration with derived pitch, roll, and yaw.
The unit was mounted on left side of the aft cabin bulkhead, facing forward. The field of view was focused to the left and downward. As such, only a portion of the instrument panel, the left segment of the annunciator panel, and some externally visible features through the helicopter's left chin bubble and left windscreen were visible. The pilot's body was not captured, nor were any of his control inputs.
The recording contained a stereo audio track. One audio channel was of a cockpit area microphone, and the other was recorded from the helicopter's intercom. The intercom track recorded continuously and captured the pilot’s voice as a “hot mic” throughout.
Throughout the recording, portions of the video playback were discontinuous and frozen. This condition had been noted previously in other investigations involving Appareo Vision 1000 devices and have been reported to the manufacturer; however, the audio playback was uninterrupted.
No annunciator lights on the visible left side of the panel illuminated during the recording.
These annunciators included:
float test, float arm, baggage door, l/fuel boost, r/fuel boost, fadec maint, engine fire, fadec ch fail, litter door, l/fuel xfr, r/fuel xfer, start fault, engine anti-ice, start, heater overtempt, a/f fuel filter, fuel valve, fuel flow,
The visible flight instruments were:
TRQ (Torque), MGT (Measured Gas Temperature), Ng, Oil pressure, Oil temperature, Transmission oil temperature, Transmission oil pressure, Fuel capacity, Amperes, Fuel pressure,
The video began at 0928:38, with the helicopter running in idle on the ground. After a series of routine radio calls, and with all visible gauges in the green range, the helicopter appeared to lift off. The helicopter remained in a low hover and the gauges continued to indicate nominal performance. About one minute later, the helicopter began exhibiting maneuvers consistent with the initiation of the exam.
Throughout the recording the pilot was audible and breathing heavily, and at 0937:10, he was heard to exclaim frustration. At this time the gauges were still showing normal values, and a radio call was audible with the person on the radio stating, "that one hit ground uh pretty good, why don't you do an orbit and start over." The pilot responded, "you got it man."
Over the next 5 minutes, the video continued to intermittently freeze, but the audio track remained continuous. The video fragments and audio indicated the pilot was performing maneuvers under the observation and supervision of the ground examiners. The pilot continued to breathe heavily while showing signs of frustration and often emitting exasperated sighs.
Eventually the ground personnel transmitted, “good job man pick up" And three minutes later the helicopter began performing maneuvers that indicated the pilot had now picked up the lineman and was performing HEC operations.
For the next 11 minutes, HEC operations continued, with the pilot communicating with the lineman as he maneuvered him around the facility. The pilot continued to breathe heavily throughout, while talking himself through the maneuvers with a strained voice.
At 0954:20, the helicopter's heading was 140° magnetic, and the instruments were still indicating nominal values, with MGT indicating 710 °C, Ng 91%, and torque 68%.
A few seconds later, the pilot exclaimed "ugh," and the torque gauge value dropped to 61% and then returned to about 65%. During this time the helicopter changed heading slightly to the left, and about 7 seconds later, a steady 2,850 Hz tone was audible that would last for the remainder of the recording. (A 2,900 Hz [+/- 50 Hz] tone represents either a low rotor rpm horn, an engine out horn, or both).
The pilot then stated, "there ya go," as the heading swung further left to about 125°. MGT continued to trend down to about 680 °C; Ng had reduced to about 88%.
The pilot then swore, and the helicopter heading swung rapidly to the right and the pilot let out another expletive. By this time, MGT had dropped to about 660 °C and Ng was unchanged.
The helicopter appeared to be descending as the heading swung further to the right. MGT had now dropped to 650 °C, and the helicopter began to show evidence of a more rapid descent. MGT then dropped to 600 °C, while Ng was indicating 82% and torque 57%.
The last frame ended about 4 seconds before ground impact with the helicopter now level with the top of a power pole just ahead.
Engine Parameters
The ECU contained an incident recording feature which was designed to provide data in support of engine troubleshooting and maintenance. The system was designed to activate after a successful engine start, then continuously record data every 1.2 seconds over a 12-second loop resulting in the last 10 sets of data always being stored. When an incident was detected, the 10 sets of data recorded preincident were saved, directly followed by an additional 40 sets of postincident data. Each data set included critical parameters such as engine history, discrete words, fault words, and key control inputs.
The ECU was tested using a Honeywell engine simulator and data for the accident sequence was extracted and time-correlated with the Appareo parametric data. The extracted ECU data included core engine and helicopter parameters along with power lever angle (PLA) and collective pitch angle.
Review of the data indicated that the ECU captured data 12 seconds before the main rotor rpm dropped to zero, which was the first event denoting an incident, and would have been about the time of impact.
The first data point in the recording indicated that the helicopter’s vertical speed was zero; however, the PLA was 102°, which corresponded to a throttle position between IDLE and FLY. Nr was at 76.6% but was decaying, while Ng remained about 87%.
About 3.5 seconds later, the PLA was at 82°, which was the IDLE position. During this time the helicopter began to descend at a vertical speed of about -500 ft per minute (fpm). Within one second, the PLA had increased back up to 142°, which would have been in the over-center position past the FLY detent. However, by this time Nr had dropped to 50%, and the MGT along with both the Np and Ng speeds began to drop. Five seconds after the FLY over-center position was selected, rapid variations in engine parameters began, along with the engine Np speed accelerating to over 100% when the Nr speed went to zero, consistent with the engine’s power turbine shaft decoupling from the main rotor system at impact and accelerating.
According to technical representatives from Honeywell, when the throttle is increased to the FLY position, if the Nr speed is still below 70%, the torque limiter will engage. This limiter was
designed to prevent an over-torque condition and corresponding yaw when accelerating from ground idle before takeoff. The limiter holds engine torque to 50% until 100% Np is reached or 10 seconds has elapsed. Therefore, even if the pilot increased the collective control, the engine would not respond because it was being held by the limiter.
Tests and Research
Engine Tests
The engine sustained minimal damage during the accident sequence and the ECU was intact. However, the FMU was damaged after being struck by the rotating engine output drive coupling during impact.
The FMU was examined and tested at the manufacturer’s facility. With the damage sustained, only a partial set of tests were accomplished; however, the unit met the nominal parameters of those tests and disassembly did not reveal any preimpact anomalies or mechanical failures.
The engine was removed, examined, and operated at the facilities of Honeywell Aerospace. No engine anomalies were noted during the examination, and the engine performed nominally when run in a test cell.
The throttle position LVDT was tested in a similarly equipped 407HP helicopter and performed within specifications.
Administrative Information
Investigator In Charge (IIC):
|
Simpson, Eliott
|
Additional Participating
|
David Jensen; Federal Aviation Administration; Oakland, CA
|
Persons:
|
Nora Vallée ; Transportation Safety Board of Canada
|
|
David Studtmann; Honeywell
|
|
John McCoy; PG&E
|
|
Alejandro Alva; Guardian Helicopters/Rotorcraft Support
|
Original Publish Date:
|
May 14, 2024
|
Last Revision Date:
|
|
|
Investigation Class:
|
Class 3
|
Note:
|
The NTSB did not travel to the scene of this accident.
|
Investigation Docket:
|
https://data.ntsb.gov/Docket?ProjectID=105065
|
|
|
|
The National Transportation Safety Board (NTSB) is an independent federal agency charged by Congress with investigating every civil aviation accident in the United States and significant events in other modes of transportation— railroad, transit, highway, marine, pipeline, and commercial space. We determine the probable causes of the accidents and events we investigate, and issue safety recommendations aimed at preventing future occurrences. In addition, we conduct transportation safety research studies and offer information and other assistance to family members and survivors for each accident or event we investigate. We also serve as the appellate authority for enforcement actions involving aviation and mariner certificates issued by the Federal Aviation Administration (FAA) and US Coast Guard, and we adjudicate appeals of civil penalty actions taken by the FAA.
The NTSB does not assign fault or blame for an accident or incident; rather, as specified by NTSB regulation, “accident/incident investigations are fact-finding proceedings with no formal issues and no adverse parties … and are not conducted for the purpose of determining the rights or liabilities of any person” (Title 49 Code of Federal Regulations section 831.4). Assignment of fault or legal liability is not relevant to the NTSB’s statutory mission to improve transportation safety by investigating accidents and incidents and issuing safety recommendations. In addition, statutory language prohibits the admission into evidence or use of any part of an NTSB report related to an accident in a civil action for damages resulting from a matter mentioned in the report (Title 49 United States Code section 1154(b)). A factual report that may be admissible under 49 United States Code section 1154(b) is available here.
READ MORE ROTOR PRO: https://justhelicopters.com/Magazine
WATCH ROTOR PRO YOUTUBE CHANNEL: https://buff.ly/3Md0T3y
You can also find us on
Instagram - https://www.instagram.com/rotorpro1
Facebook - https://www.facebook.com/rotorpro1
Twitter - https://twitter.com/justhelicopters
LinkedIn - https://www.linkedin.com/company/rotorpro1