Aug
21
2023
|
|
Posted 1 years 364 days ago ago by Admin
|
|
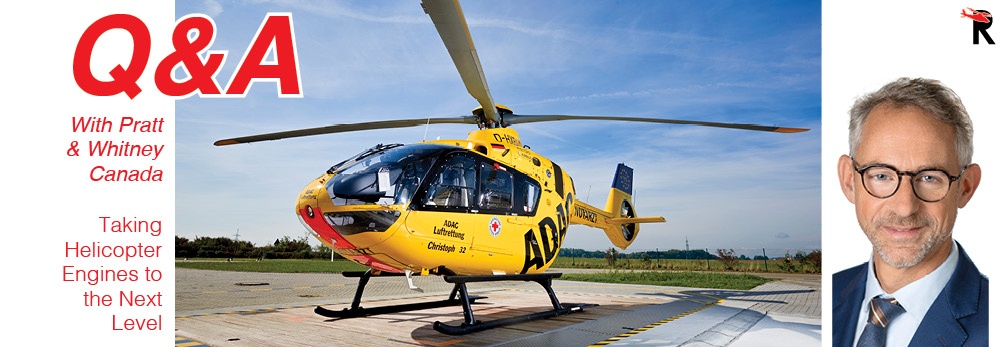
All around us, technology is changing. The helicopters of our youth are dinosaurs compared to today’s aircraft. The modern engines that power these helicopters have become sophisticated, digitally controlled power plants designed to optimize performance and reliability while also reducing fuel consumption and greenhouse gas emissions.
To gain insights on where helicopter engine technology is headed, Rotor Pro spoke with Nico Chabée, vice president of sales and marketing at Pratt & Whitney Canada.
Rotor Pro: What tech are helicopter engine manufacturers and MROs currently using to become more fuel efficient and reduce carbon emissions?
Nico Chabée: Pratt & Whitney's sustainability strategy is centered around three pillars: smarter, cleaner, and greener.
We have been a leader in propulsion systems and technology for decades. In our view, the challenge that climate change presents to the world is also an opportunity for the global aviation industry to make change through new technology.
For example, we are continually advancing fuel efficiency in aircraft propulsion systems. We are conducting ground- and flight-testing of traditional engines as part of a process to ensure they are compatible with higher blend ratios of sustainable aviation fuel (SAF). Combined with engine efficiency gains, wider adoption of SAF will be critical to reducing the net carbon emissions of aviation by 80%.
Rotor Pro: How can SAF have an impact on reducing greenhouse gasses?
Nico Chabée: From an industry standpoint (including ICAO and others), the immediate and most efficient path to de-carbonization would be drop-in SAF up to a 50% blend, which does not require any technological or infrastructure changes to the current operating fleet. All Pratt & Whitney Canada engines have been 50% SAF compatible for more than a decade. We are working with a variety of customers and OEMs on moving our engines to 100% SAF compatibility and we have conducted a number of test flights that have produced excellent results.
Of course, the mass use of SAF is predicated on the availability and pricing of SAF blends today. This is even more specific to the rotorcraft industry, which will have other challenges to implement the other CO2 reduction options.

Rotor Pro: What else is Pratt & Whitney Canada doing to reduce engine emissions?
Nico Chabée: We are exploring the use of alternate power sources including electric, hybrid-electric, and hydrogen.
Hybrid-electric technology will offer even more fuel efficiency and reduced emissions. In December 2022, Pratt & Whitney completed the first engine run of the regional hybrid-electric flight demonstrator, marking a key milestone towards flight testing, targeted to begin in 2024. The propulsion system's initial run took place at Pratt & Whitney's innovation facility in Longueuil, Quebec, and performed flawlessly.
We believe that whatever we learn about power conditioning, about batteries, and about making the system work as a propulsion system onboard a real aircraft will be transferable to the helicopter market segment.
Pratt & Whitney Canada was also the first OEM to offer a carbon offsetting service. Our carbon offset service is a transparent, cost-effective, and flexible way for all Pratt & Whitney Canada-powered operators, and operators of non-Pratt & Whitney Canada powered aircraft to support mixed fleet customers, to offset the carbon footprint of an aircraft and support their sustainability objectives. To make this approach work, Pratt & Whitney Canada estimates the CO2 emissions based on the engine model and reported flight hours and compensates the emissions by sourcing high quality carbon offset credits from South Pole, a globally recognized carbon offset provider.
This solution reinforces Pratt & Whitney Canada's long-standing commitment to offer environmentally responsible products and solutions. This year we invested in a diverse group of Gold and Verified Carbon Standard offset projects and focused on projects that have a high social impact:
Rotor Pro: How do you expect the transition to greener helicopter engine technology to unfold over time? What tech will OEMs be transitioning to become more fuel efficient and reduce carbon emissions in the future? SAF, electric, hydrogen?
Nico Chabée: Realistically, from a rotorcraft standpoint, it may be a step evolution that includes/requires all of the above with 50% blended SAF being the first, closely followed by Jet X or 100% SAF.
The introduction of mild electrification will also appear in parallel, with limited mission enhancements, which will enhance takeoff and safety (auto-rotation). As the battery density increases, this mild-electrification may move to higher use of hybrid-electric battery solutions.
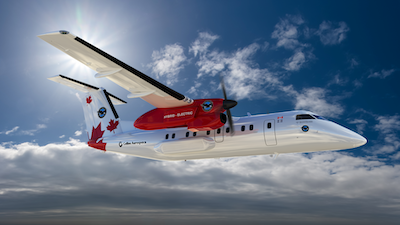
This will be followed by hydrogen fuel cells being introduced in the next 10-20 years.
Rotor Pro: What does the long-term road map to decarbonization look like for helicopter engine OEMs?
Nico Chabée: Using less of any fuel, whether it's traditional Jet A, SAF, battery power, or hydrogen, will always be the goal.
At the OEM level, hybridization offers some interesting trade-offs for twin-engine helicopters, where there is a potential to resize the power plant for improved cruise efficiency and supplement with electric power to cater for the OEI scenarios. For example, in 2023, Pratt & Whitney Canada successfully conducted an 100% SAF flight test with PW127M engines on a Braathen Regional Airlines' ATR 72-600 aircraft.
At the customer level, one of our long-term customers is looking for more immediate results through the use of SAF. ADAC Luftrettung, a German air rescue operator, is in the process of extending SAF usage to its fleet of P&WC-powered helicopters. In late 2021, ADAC announced its plan to operate using SAF at blends of 30-40% over the course of 36 months, the program will set one of the most extensive operational SAF usage cases for the sector.
Rotor Pro: What are the challenges associated with achieving these goals?
Nico Chabée: In terms of SAF, scalability appears to be the main challenge, followed by fuel certification to a lesser degree.
Hybridization and electrification challenges primarily include battery technology – specifically energy density and infrastructure around battery charging and replacement.
There is a fair bit of work left to do with regulators when it comes to certification bases for disruptive technology and airspace concerns in and around densely populated areas.
Based upon the current generation of helicopters, innovative technology insertion will be multiplexed (hydrogen/electric). In the short term, we see SAF as the major contributor to the reduction of carbon emissions.
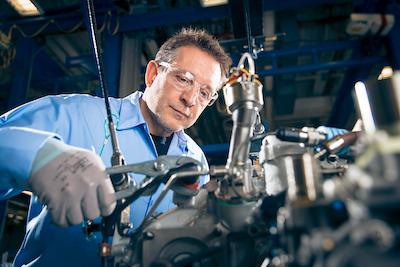
The IKO Corsia Agreement provides additional market measures for aviation to leverage offsets with other industries. We will be working closely with OEMs who are looking at innovative next generation helicopters to design propulsion systems which will meet their requirements.
Rotor Pro: What real progress has been made to reaching these goals so far?
Nico Chabée: As noted previously, all P&WC engines are compatible with up to 50% SAF blends, which is a success in and of itself.
We are continuing to participate in the development of the appropriate standards toward 100% SAF (for example, working with ASTM International, formerly known as the American Society for Testing and Materials) and its possible implementation around the 2025 timeframe. This will enable engine OEMs, airframers, and MRO organizations to support a further reduction in CO2 emissions with hopefully no changes to technologies, major infrastructure impacts, or operational and maintenance processes.
We continue to communicate with our customers and operators to educate them on our current compatibility levels, and have a multi-year plan to reach compatibility with future unblended SAF shortly after fuel certification.
Electric and hybrid-electric vehicles have successfully flown demonstrators. Developing and optimizing vehicle performance for production platforms and their eventual certification are the next challenges. The industry will need to continue to mature the technology readiness of a long list of enablers.
And, as noted previously, we are working on a number of technology fronts that includes hydroelectric and hydrogen, among others.
Our customers expect us to look beyond what a demonstrator can achieve, to ensure the next generation of propulsion systems offer equal or better safety and reliability, with similar mission capability/effectiveness for the vehicles they power, to the latest certification standards.
Rotor Pro: In closing, where does Pratt & Whitney Canada stand in terms of its total helicopter engine portfolio?
Nico Chabée: This year, P&WC is celebrating two major milestones — reaching 1 billion hours of flight across its engine fleet and 60 years of the PT6 excellence. The PT6 is unmatched in engine performance, reliability, and dispatch availability, and has reached 500 million flying hours, which accounts to half of the 1 billion milestone.
With more than 64,000 PT6 engines produced since its introduction in 1963, it powers over 155 different aviation applications.
The PT6 engine remains at the forefront of the aviation landscape, bringing breakthrough achievements in performance, control systems and data intelligence. Today's PT6 is up to four times more powerful, has a 50% better power-to-weight ratio and up to 20% better specific fuel consumption compared to the original engine. Each new model is developed and designed with a specific mission, platform and customer in mind, while pursuing a reduced environmental footprint.
The PT6 engine's relentless technological evolution has never been more apparent than in recent years. The latest engine family, the PT6 E-Series™, is the first with a dual-channel integrated electronic propeller and engine control system in general aviation.
The PT6 is also the only turboprop engine in the world to be approved for single-engine instrument flight rules (SEIFR) in commercial passenger flights in Europe, North America, New Zealand, and Australia.
Rotor Pro: Thanks for your time!
Nico Chabée: You’re welcome.
READ MORE ROTOR PRO: https://justhelicopters.com/Magazine
WATCH ROTOR PRO YOUTUBE CHANNEL: https://buff.ly/3Md0T3y
You can also find us on
Instagram - https://www.instagram.com/rotorpro1
Facebook - https://www.facebook.com/rotorpro1
Twitter - https://twitter.com/justhelicopters
LinkedIn - https://www.linkedin.com/company/rotorpro1