Nov
29
2021
|
|
Posted 3 years 265 days ago ago by Admin
|
|
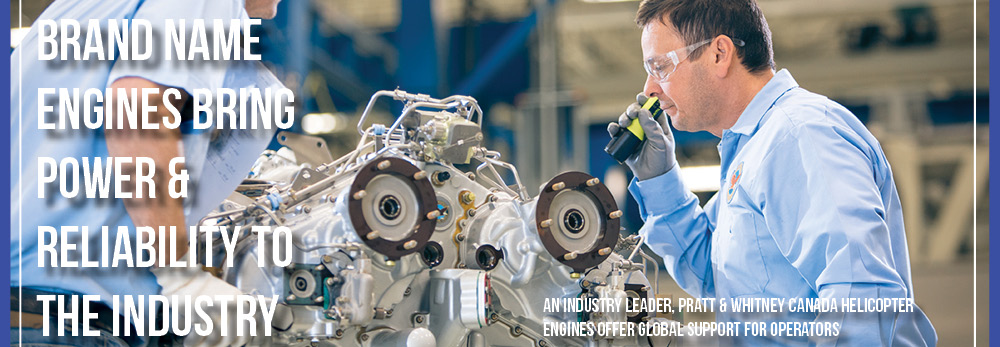
VIEW IN ROTORCRAFT PRO SEP/OCT 2021
There is a reason that Pratt & Whitney Canada helicopter engines are well-known. It could come from the outstanding customer support, the innovative engine updates, the 24/7 availability with over 2,000 professionals in their Global Service Network, or perhaps overall reliability. Now, in addition to these attributes, they are highly invested in sustainable practices.
Simply put, Pratt & Whitney is a household name as a global aerospace leader. The company was started in the mid-1860s by Amos Whitney and Francis Pratt, a pair of mechanical engineers bent on entrepreneurship, training apprentices, and filing patents for good ideas.
Pratt & Whitney Canada (P&WC), a business unit of Pratt & Whitney, introduced their first helicopter engine in the early 1970s, according to Nicolas Chabée, vice president, helicopters, Pratt & Whitney Canada. He said that the first engine was the PT6T TwinPac™ that brought, "a new measure of safety to helicopter aviation."
Fifty years later, they have produced 17,500 helicopter engines. Chabée said that 10,000 are still flying today. "We are the recognized leader in light, medium, and intermediate twin helicopters," Chabée added.
Any company with the longevity of Pratt & Whitney has done it with a special secret. Many aerospace and defense companies have failed through the years. Perhaps it is because of the inability to secure defense contracts or poor quality from employee commitment. Quality and reliability are critical in this industry. In the case of P&WC, there are many reasons why they are succeeding today.
Vice President of Customer Service Satheeshkumar Kumarasingam is a man who is turning around impressive customer service programs. They offer global support through more than 50 MRO owned and designated facilities located on five continents. They have over 100 field support managers and 100 mobile repair team technicians, who "travel to meet customers in need," according to Kumarasignam.
He added that they've recently opened a new MRO facility north of Rio de Janeiro in Belo Horizonte, Brazil.
He said, "This means turnaround times will be significantly truncated with no need to ship an engine across international borders. For the customer, it means less downtime and reduced engine-rental requirements and costs."
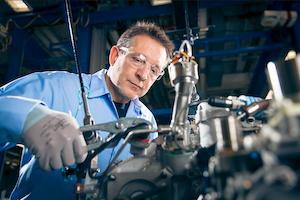
The P&WC website, www.pwc.ca, said, "We are fully equipped to meet our operators' engine needs – sales, rental exchange – and to support the continuity of customers' operations if it becomes necessary to remove an engine for maintenance. New spare engine solutions such as long-term leasing are providing attractive alternatives for customers who want exclusive access to spare engines while keeping ownership costs down."
Chabée said another reason for success is the versatility of the helicopter engines. The P&WC engines “fly diverse missions from search and rescue to VIP transport, from firefighting to sightseeing, and from emergency medical services (EMS) to windmill and power-line maintenance."
Chabée said that over 40% of their engines are in the security and defense markets. He said he sees industry growth in refreshing aging helicopter parts, and product expansion in countries like China.
Of course, it doesn't hurt that there are 1,500 operators flying helicopters with their engines worldwide. Operators are buying maintenance services with aftermarket support. They offer variety in their aftermarket support based upon the "operator's mission, model, ownership, and lifecycle needs," said Chabée.
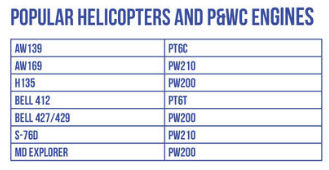
Most important though, is the missions that are flown using P&WC engines. The missions impact the safety and social being of communities. In many instances, helicopters that we power help save lives and project communities every day," he added.
While the engines are a critical part of the aircraft, they are going into aircraft with significant OEMs, Airbus, Leonardo, Bell, MD Helicopters, and Sikorsky. The OEMs sell directly to the end-user. But Chabée added that operators still come directly to P&WC for customer support, as provided through the global service network.
Now, they are also offering AW169 Performance Packs. These support the twin-engine 4.5-ton class helicopter. The engines feature "dual channel Full Authority Digital Control (FADEC) that delivers an exceptional sense of operation, maintenance diagnostics and other control features." The FADEC improvements are software-driven, and the company said that they are always looking at ways to improve the service performance of existing engines. Overall, FADEC increased payload and flight envelopes up to 20,000 feet.
In 2020, Pratt & Whitney Canada launched a Carbon Offset Service for business jet customers enrolled in its Eagle Service™ Plan (ESP™) maintenance program, making it the first engine manufacturer to offer this type of service. As a result of the positive response, the company is now also expanding its availability to helicopter customers enrolled in ESP™.
In addition to its Carbon Offset Service, the company’s website contains information about how operators can reduce their carbon footprint, to be more sustainable, "Sustainable aviation fuel (SAF) is one of the solutions available today for in-service engines to address the decarbonization challenge. All P&WC engines are ready to operate with SAF at up to a 50% blend, and the company is working towards making engines 100% SAF ready in the future – SAFs have a key role to play for decarbonizing aviation and reaching industry goals. SAF, made from by-products of other industries, supports carbon reduction by drastically reducing CO2 emissions across its life cycle compared to conventional fossil-based jet fuel. If used alone, SAF can reduce emissions by up to 80%. In its pure form, however, it is not yet able to meet the standards set by the aviation industry."
Also, Kumarasingam said that building reliable engines and offering maintenance packages helps with sustainability because operators can fly longer with the same equipment. He added, "Reliability is an integral element of our overall brand and our image in the marketplace. And, yes, reliability is very important to our customers."
Another technology they've implemented is Oil Analysis Technology, which Kumarasingam said is available on several models. "The technology is up to a hundred times more sensitive than other engine oil monitoring solutions. It analyzes trace amounts of metallic debris from oil-wetted engine components such as bearings, gears, and carbon seals to identify potential issues.”
Enhanced technology is a win for many aerospace companies. In addition to the technology, Kumarasingam said customers are becoming more sophisticated in their needs. He said their engine customers are less focused on major maintenance events, "Hot Section Inspections, Overhauls," and are more focused on the line support required between events.
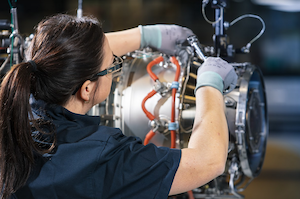
"So, it was for this reason that we built the Designated Maintenance Facility (DMF) network, which offers rapid, local response to operators, helping get them back to service with minimal delay. We now have 17 DMFs around the globe," he said.
An article in Pratt & Whitney’s Airtime blog states, "Thanks to advances in materials and technology and the continuous improvement of our products based on field experience, engine maintenance intervals for major refurbishments are now longer than ever before."
According to the article, they offer in-country DMFs in "China, India, Russia and Brazil (which) enable faster service response times through simplified logistics and the elimination of cross-border issues."
Although the DMFs, established starting in 2017, are pre-pandemic, they say that it has been a precursor for the future of customer support.
"Over the past year, restrictions on international travel have made obtaining maintenance services more challenging for many in the aviation field. During this time of harder borders and logistical barriers, P&WC’s network of Designated Maintenance Facilities (DMFs) is demonstrating the value of offering tailored in-country services," according to the article..
Further, Ismael Rhissa Zakary, general manager, customer service center Europe, said in the article, "European countries such as Spain and Italy have been tremendously affected by the pandemic. Our DMFs were able to intervene very quickly and provide support when our technicians, most of whom are based in Germany and the United Kingdom, were unable to travel in person."
In summary, Pratt & Whitney Canada helicopter engines are about so much more than the actual engines. The company has proven longevity, but they haven't relied solely on an original idea of well-constructed engines. The organization has continued to innovate customer support programs, like the DMF locations worldwide, while keeping an eye on the future of customer needs and sustainable operations.
TO READ MORE ARTICLES IN THIS ISSUE