Jul
05
2021
|
|
Posted 4 years 43 days ago ago by Admin
|
|
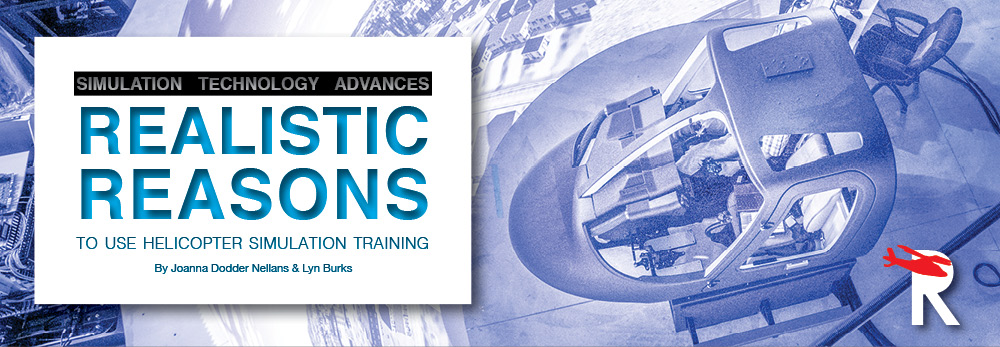
All over the world, helicopter flight training is at the heart of every facet of helicopter operations. Whether training a new hire, or providing recurrent training to seasoned pilots, the quality and quantity of training can have an impact on areas like accident rates, safety in operations, and direct operating costs.
As is in most industries, technology is advancing rapidly and making simulation training more realistic and cost effective. It used to be that only larger helicopters like the Sikorsky S76, Bell 412, or Airbus Super Puma would have simulators available for clients to train in. Now even light twins such as Airbus H135 and single engine helicopters such as Bell 505, Airbus H125 and Robinson R44 have simulators available for training.
In this article we turn to four companies and ask them to share their expertise in the areas of training and manufacturing. On the subject of “reasons to use simulation in helicopter training” we turn to global training providers, FlightSafety International and Helisim LLC.
To learn more about the top technology advances that simulator original equipment manufacturers (OEMs) are using to enhance realism and improve training outcomes, we lean on one of the oldest simulator manufactures in the world, FRASCA International, as well as a newer company to the market, Entrol.
THE TRAINERS
In business since 1951, FlightSafety International provides both fixed-wing and helicopter training using advanced-technology simulators, to commercial, government and military organizations worldwide. FlightSafety has 1,800 instructors working at learning centers in 11 countries. Additionally, they provide 1.4 million hours of training annually on 135 aircraft models.
Helisim LLC, although a younger company, is extremely capable and dedicated to providing high quality training to its clients. Helisim is the training arm for Airbus Helicopters and is a consortium of agencies which includes Airbus Helicopters, Thales AVS, and the Défense Conseil International. The company provides training on H125, H135, H145, AS365 N2, H155, H175, AS332, H225, NH90 and very recently on the new H160.
Rotorcraft Pro asked each of these companies to provide us with the top reasons why operators should use simulators for helicopter training.
SAFETY: Effective and comprehensive training involves reviewing and practicing normal procedures, and more importantly, abnormal and emergency procedures. The room for error while practicing these procedures in the aircraft is marginal. In a simulator, this potential danger is removed. Emergency and abnormal procedures can be practiced under a broad variety of weather and environmental conditions without risk in the simulator; not so in the aircraft.
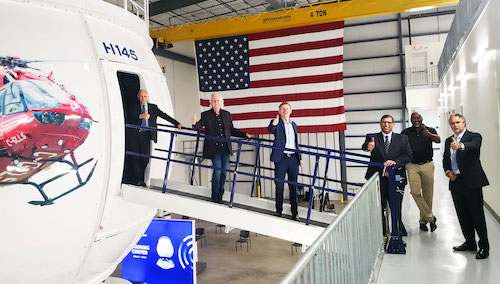
FIRST H145 FULL FLIGHT SIMULATOR PUT INTO SERVICE IN NORTH AMERICA
The Helisim Simulation Center, located inside the Airbus Helicopters Inc. facility in Grand Prairie, Texas, recently inaugurated a new Thales Reality H full-motion flight simulator, the first of its kind in the region.
This represents a major international expansion of France-based Helisim, a joint venture of Airbus Helicopters, Thales, and DCI, which brings 20 years of experience in simulation training with Airbus helicopters.
“With this new training center, Helisim is able to offer the best simulator-based training to H145 operators,” said Jean-Charles de Troy, managing director of Helisim LLC. “With outstanding equipment and software implemented, including an OEM simulator data package, along with integrating Airbus helicopter flight instructors, our goal is to offer a reliable and true-to-mission training experience to H145 pilots.”
The North America training center is one of 18 training and simulation centers run by Airbus Helicopters worldwide and trains upwards of 1,500 pilots and maintenance personnel every year in Grand Prairie, which, as part of the Dallas-Fort Worth metroplex, has seen significant growth and local investments in recent years.
IMPROVED EFFECTIVENESS OF TRAINING: When training is done in-aircraft, the trainee and the instructor must imagine certain conditions exist. In the simulator, abnormal and emergency events happen just as they would in the actual aircraft. No need to pretend. No need to substitute imagination for reality. Procedures can be practiced repeatedly without delays from air traffic, weather conditions or ATC. The trainee and instructor can focus on the task at hand without distraction. Training in a simulator is far more comprehensive and thorough than it could ever be in the actual aircraft.
“We all learn best from firsthand experience, and simulators allow for realistic exposure to challenging situations which may occur in flight operations. While in-aircraft training meets regulatory requirements, for safety reasons, it does not allow pilots to experience the full spectrum of potential scenarios, and therefore limits the pilot’s preparedness. Practicing critical failure events in realistic conditions in a simulator prepares pilots to manage real-world anomalies and malfunctions with precision and confidence.” - Richard Meikle, EVP, Safety and Regulatory Compliance, FlightSafety International
REDUCED TRAINING COSTS: When all costs are considered, simulation-based training is the far better value. Direct operating costs, additional maintenance requirements, unnecessary risk exposure and time lost to air traffic or weather considerations all inflate the true cost of in-aircraft training. Well trained crews merit lower insurance rates. In some cases, insurance companies may not insure low-time pilots, unless they train in simulators with a professional training organization. One accident/incident in the aircraft can easily cost much more than an entire year’s worth of simulation-based training.
“Simulation training is cost effective, especially for medium to heavy helicopters. There is no risk of damaging your helicopter during training, and your aircraft will remain operational and generating revenue.” - Jean-Charles deTROY, managing director, Helisim LLC
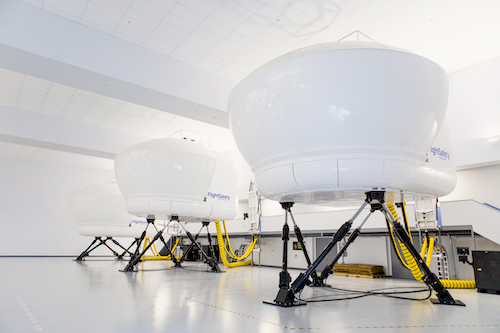
Photo Courtesy of FlightSafety International
DEEPER UNDERSTANDING OF COMPLEX SYSTEMS: Modern aircraft offer reduced pilot workload, but only when the systems are in operation. When these systems become degraded or inoperative, the pilot's workload can increase dramatically. Without adequate understanding of these systems and proper training, the pilot(s) may not react properly to a system degradation or failure. Simulation training allows for in-depth training on aircraft systems and indications of failure/degradation in a low-stress environment.
SCENARIO BASED TRAINING: This kind of training will allow you to cover a broad spectrum of conditions and factors that could lead to an accident, such as weight, weather, high density altitude, night operations, and the element of surprise. Scenario based training is an ideal tool for single- or multi-crew operations.
LESS ENVIRONMENTAL IMPACT: Modern simulation training is fully electric and does not introduce any noise or environmental pollution. It offers lower emissions, a lower carbon footprint and zero noise pollution. No more noise complaints from neighbors.
REDUCED LIABILITY EXPOSURE: In-aircraft training creates unnecessary exposure to incidents and accidents. This activity subjects aircraft and crew to added risk, which in turn generates potential liability for the aircraft operator. Simulation-based training provides a safe, focused and realistic training environment…far superior training with zero risk involved.
REDUCED AIRCRAFT WEAR: Routine operation of any aircraft generates the need for routine maintenance. In the training environment, the aircraft is easily subjected to excessive wear and tear creating the need for additional maintenance and servicing. Hard landings, engine and system exceedances along with other training-related incidents can reduce the useful life of an aircraft and cause premature component replacement. Training in a simulator reduces wear and tear on the aircraft, which in turn represents a reduced overall lifetime maintenance cost.
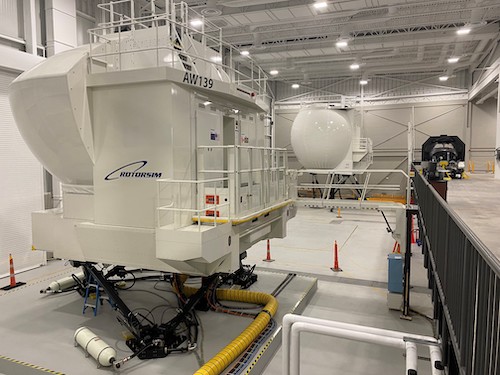
LEONARDO OPENS NEW U.S. TRAINING ACADEMY
Leonardo recently opened their brand new, state-of-the-art Helicopter Training Academy, located on their existing campus in northeast Philadelphia that also includes production, support, and administrative functions for the United States.
The new Academy in Philadelphia is part of an $80 million investment in United States operations that will provide training services for a growing demand and need for pilots, cabin crews, and maintenance technicians across North and South America. The Training Academy in the U.S. will mirror the services provided by its sister facility in Sesto-Calende, Italy, offering ground, air, and virtual training and also leverages simulator capabilities jointly developed by Leonardo and CAE and operated by their Rotorsim JV. The Academy, which is already up and running for customers, features training services for the AW119, AW169, AW139 models, and will also be home to the training services for global customers of the world’s first tiltrotor set to receive civil certification–the AW609.
“We purposely co-located the Academy next to our main production, support, and administrative offices because we wanted to not only provide cutting-edge training with modern technology to our customers, but also give them an inside view of our organization, our culture, and how our product is made and maintained with a constant emphasis on quality and safety” said Bill Hunt, CEO of AgustaWestland Philadelphia Corporation and managing director of Leonardo Helicopters U.S.
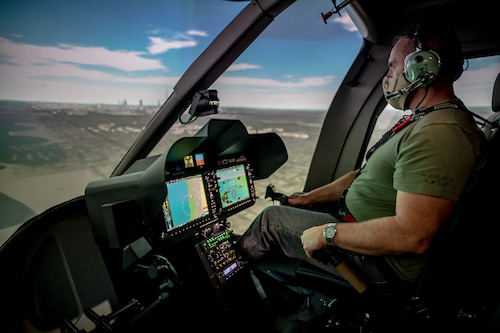
Photo Courtesy of Entrol
THE MANUFACTURERS AND TECHNOLOGY
On the manufacturing side of the equation, we again spoke to two companies, similar in circumstance to the training businesses, in that one was much more seasoned, while the other was newer to the market.
Founded in 1958 by aviation pioneer Rudy Frasca, Frasca International was born from a passion for flying and a goal to make aviation safer. Today, the 130 employees of Frasca have built more than 3000 fixed- and rotor-wing simulators which are in service in more than 70 countries.
Entrol, headquartered in Madrid, Spain, has been manufacturing both fixed-wing and helicopter simulators since 2005. They manufacture EASA approved simulators (FNPT II-MCC and FTD Level 2) and FAA approved devices (from AATD to FTD Level 7) and have a portfolio of 20 different simulators to date.
Rotorcraft Pro asked each OEM to share what they believe are the top technology advances in helicopter flight simulation, and their benefits to training outcomes?
IMPROVED PC COMPUTING AND PROCESSING POWER: Smaller chips, faster processors, more RAM, etc… all factor into several important dimensions of helicopter simulation. Those dimensions would be: flight and systems modeling, improved equations of motion (EOM) relating to the 6 Degrees of Freedom or 6 DoF. EOM are the equations that translate the aircraft’s physical flight characteristics into mathematical equations.
“Thanks to the technological evolution of graphic boards, the virtual world where pilots fly in flight training devices is more realistic than ever. Thanks to that, pilots are more immersed during training, which improves the quality of the lessons.” - Nacho Navacerrada, business manager, Entrol
ADVANCES IN VISUAL SIMULATION AND CAPABILITY: Because so much of a helicopter’s mission is in VFR conditions or relies on visual elements – because the pilot needs to see that log landing pad, or that hospital roof-top – this is a critical element. When we look at the visual sub-system elements, the main technology there is graphics cards and their graphic processing units, projector technology, and the image generators (IGs) that render the simulator’s visual – the IG is what draws the out-the-window view of all flight simulators. Projector technology today allows for very large, uninterrupted fields of view (FOV) so that we can recreate the same visual environment one would see when sitting in the helicopter.
AVIONICS SIMULATION AND INTEGRATION: The ability to accurately integrate advanced avionics into simulation is a clear and obvious advantage to training outcomes. Since the avionics explosion in aviation of the mid-90s, many of these advanced systems have found themselves adapted into helicopter platforms too. Today, fully integrated avionics with GPS, moving maps, 3- and 4-axis automatic flight control systems (AFCS), and terrain warning systems are commonplace in both twin- and single-engine helicopters.
ADVANCED MOTION SYSTEMS: Helicopter motion systems and algorithms and vibration cues specific to rotorcraft and the hardware systems that reproduce these cues are critical to improving realism in the cockpit. Many earlier helicopter simulators that used large Level D motion systems also used the EOM for the system supplied by the motion system OEM. In many cases, these 6-DoF EOMs were optimized for fixed-wing flight characteristics, and did not focus on reproducing the subtle nuances or dynamics of rotorcraft aerodynamics. Motion bandwidth for these older systems would typically be in the 10-12 Hz range because of all the weight and inertia involved with these large systems. With today’s short-stroke 6-DoF motion and cueing systems, motion cues are delivered at 60 Hz, so the “seat of your pants” feel is being delivered at a much faster rate. Especially with light, unaugmented helicopters, we can feel the aircraft moving before any visual or instrument clues tell us that.
ADVENT OF EXTENDED REALITY: Virtual, mixed, and augmented reality applications, or the conglomerate of those techs - deserves a spot here with a place-holder for future development. Early implementations of extended reality technology in aviation training have shown some promise. There are certainly areas that have benefitted with improved training options via something that is more deployable and less costly, so that practicing specific tasks (with positive transfer) can be done more frequently.
“The amalgamation and cohesive use of technological advancements for realistic mission training cannot be overstated. Many of these technologies listed cannot stand on their own.In a flight simulation environment, if any of these elements doesn’t perform at very high levels, in a cohesive fashion, with the other elements of the simulation, then chances are you are going to miss out on the training value that could be achieved otherwise.” - Randy Gawenda, business development manager, FRASCA International
MACHINE LEARNING AND BIG DATA: Big data and machine learning algorithms will undoubtedly play a larger role in the future with the goal of enhancing pilot training programs by evaluating the collected data of a pilot’s performances during simulated flight lessons.
IMPROVED FLIGHT MODELING ACCURACY: Current FFS and FTDs feature aircraft type specific flight models to meet regulations and the training provider’s requirements. Significant data is collected for flight modeling by flying the real helicopter. With more accurate data and flight modeling, FFS and FTDs will behave like the real helicopter, and therefore pilots can perform normal and emergency procedures more safely and cost-effectively.
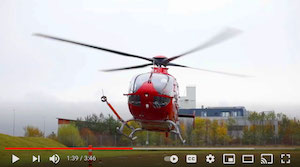
VIEW ENTROL VIDEO

SIMS IN PRIMARY TRAINING REDUCES TIME TO HOVER
Anecdotally, there's evidence that use of the FRASCA TH-57 FTD (Flight Training Device) for learning initial helicopter flight skills is showing positive results for new U.S. Navy helicopter pilots. Recently the Navy has rolled out another piece of their new “bridge” curriculum under the TH-57 ATS (Aviation Training Services) contract. The Level 6 and 7 FTDs were built by Frasca for FlightSafety International – Defense who provides the simulators, instructors, and maintenance under the Navy contract.
The first students are working through the TH-57B contact phase of training. In the past, new pilots would take about 3-4 aircraft flights before they could hover, which is 6-8 hours of aircraft time. The first student through the “bridge” curriculum, which teaches hovering tasks in the Level 7 FTD first, came to the flight line and was hovering the aircraft in 20 minutes. Due to leveraging existing Frasca COTS rotorcraft technology of Level 7 FTDs with Frasca’s short-stroke Motion Cueing System (FMCS), the devices and modified curriculum are starting to show signs of validation. This will stream-line the training pipeline and provide training efficiencies that were previously thought impossible. In the past, there were widely held doubts that hovering could be taught in a simulator of any kind. However, anecdotal evidence is changing that misconception.